Sheet metal forming through simulations
The goal of this investigation is to predict deformation, stress relaxation and thickening of component's walls
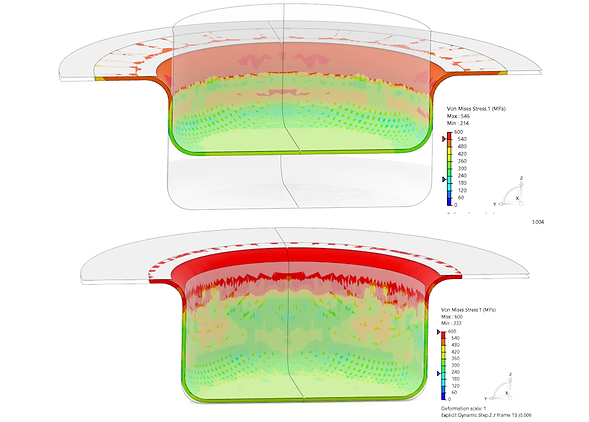
A client from the manufacturing industry approached us to evaluate the performance of a sheet metal forming process. Their goal was to predict the deformation and stress relaxation effects accurately while ensuring the final product met strict thickness and durability requirements.
Using finite element simulations, we incorporated creep material data to model the long-term stress relaxation behavior during the forming process. This approach allowed us to capture the intricate material responses under high pressure and temperature conditions. Additionally, we analyzed the post-deformation thickness of the sheet metal to ensure uniformity and compliance with design specifications.
Our analysis provided the client with critical insights into the forming process, helping them optimize parameters to improve product quality and reduce waste.
For manufacturing processes that demand precision and efficiency, advanced material modeling and simulations are invaluable tools. Contact us to explore how we can support your production challenges.